Printing with Modifiers and Mordants
By Lydia Brockman
I started working with natural dyes a little over a year ago. I had the unique privilege of beginning my studies of natural dyes through chemistry classes lead by Dr. Emily Gaul at the School of the Art Institute. During my second chemistry course with Dr. Gaul, Chemistry of Metals, I studied metal salts and their use as mordants in the dye process. Mordants create a positive charge that allows the dye molecule to bond to the fiber, creating a richer, brighter, stronger color. For my final project I experimented with alum and iron mordants and with the differences that result from shifts in the pH of dye baths.
While tap water varies from place to place, the normal pH of Chicago water is around six. By introducing an acid or alkali, the bath will shift lower or higher on the pH scale. Some examples of alkalis are baking soda, soda ash, and lye. When handling lye always wear gloves and goggles, because lye can irritate or burn the skin and damage sight. An alkali bath will usually produce a pinker tone whereas an acid will produce a yellower tone. Acid modifiers include vinegar, lemon juice, and cream of tartar.
The success of my final project in my Chemistry of Metals class lead to an independent study the following semester where I continued to work with pH modification, this time for screen printing. Screen printing allows mass production of image or text on nearly any flat surface. The screen is coated with emulsion and exposed to light with the image or text of choice blocking the light from exposing and hardening the emulsion on the screen. The un-hardened emulsion then can be removed and ink can be squeezed though the tiny holes in the screen that are not blocked by the hardened emulsion. Instead of using ink to create an image though the holes on the screen, I used modifiers and mordants. I thought that if the mordants and modifiers were mixed into a paste much like the consistency of ink and printed, the fabrics could then be dyed and only the screen printed portion would be altered by the mordant or modifier. I began by burning an image on my screen of a mannequin that I use in my own artwork. After the screen was completed, I mixed the paste to be pulled though the screen to create the image, and combined one cup of Nazdar Clear Base (commonly used for screen printing) with one tablespoon of iron mordant. I then printed the iron and clear base combination on organic cotton and allowed it to dry for thirty minutes.
The next step entailed preparing a dye bath of 6% pomegranate and 4% alum acetate which was based on the weight of the fabric sample. The iron-printed organic cotton sample was then placed in the dye bath for one hour, then rinsed and left to dry overnight. The iron-printed organic cotton sample print changed color as anticipated.
Following this, I prepared the pH modifiers of soda ash (alkali) and cream of tartar (acid), in the same way as the iron and clear base combination; one cup clear base to one tablespoon modifier. The cream of tartar dissolved nicely in the clear base, however the soda ash needed to be dissolved in four ounces of hot water, and then added to the one cup of clear base. It was a bit too wet for screen-printing, so I worked out water by smearing it over the parchment paper, yet still did not achieve the correct consistency. I then printed the soda ash (alkali) and cream of tartar (acid) samples on organic cotton and allowed the samples to dry for thirty minutes.
I prepared two dye baths of 4% madder root and 2% alum acetate. The cream of tartar (acid) and the soda ash (alkali) samples were placed in separate dye bathes to avoid the acid and alkali contaminating each other. The samples were dyed for one hour, rinsed, and left to dry overnight. However, the colors of the alkali- and acid- printed samples were not as strong as the iron-printed sample. Possibly, the clear base and modifier combination was too strong, making the bath too alkaline or too acidic. Or perhaps the image was too complex, and thus deteriorated quickly. Finally, I was never able to achieve the correct consistency for printing with the soda ash and the clear base. This could also account for the poor print quality.
Now, as a graduate of the School of the Art Institute, I continue to experiment with other fibers such as silk, or linen, and am inspired by iron print application. The minor setback with the modifier print application has only made me want to experiment more, excited for what is to come.
Soda ash print overdyed with madder | Iron print overdyed with Pomegranate |
![]() |
![]() |
Photograph Copyright by Lydia Brockman | Photograph Copyright by Lydia Brockman |
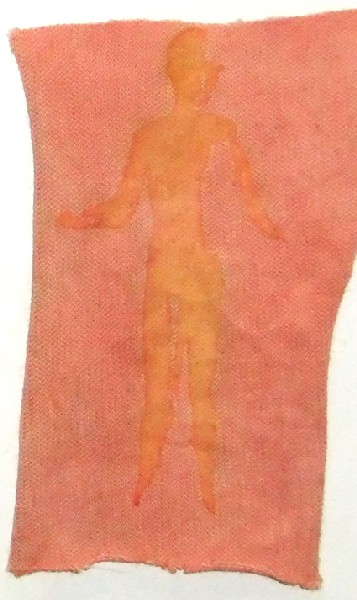