The Silk Threads of Khiva
by Nancy Zeller
On October 14th and 15th, 2006, I took part in a workshop at the Snow Farm, Williamsburg, Massachusetts, which brought together a partnership of artisans from Khiva, Uzbekistan and American artisan mentors to teach and share the Khiva traditional crafts. It was a project that took an enormous amount of time to coordinate, fund and implement. There were three crafts taught at Snow Farm, each using the silk threads of Khiva; natural dyeing, embroidery and rug weaving. The workshop was an experience, and not one I shall soon forget.
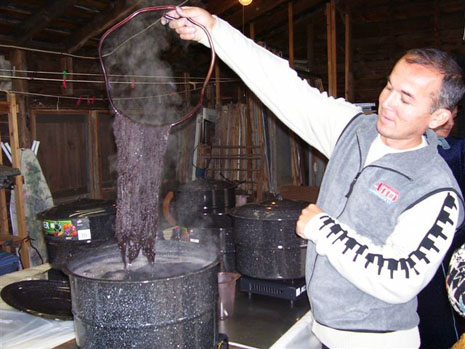
Uzbekistan is situated in Central Asia, between the Aral Sea and the mountains of Thian Shan. Previously part of the USSR, it became independent in 1991. Uzbekistan is the third largest producer of silk in the world after China and India, and has been part of the Silk Road (the trade routes that linked the West to China and India) for centuries.
Khiva, an ancient oasis city, has long been a center for textile arts. The story goes that this ancient city was founded by Shem, the son of Noah. The city dates back to at least the 7th century A.D. and probably earlier. Khiva has been called the most perfectly homogenous example of Islamic architecture in the world. The old city (Ichen Xala) is surrounded by massive mud coated walls and the former Islamic schools within have been transformed into workshops and bazaars catering to the annual tourist trade. Within the walls of Ichen Xala work the artisans of the Khiva Silk Carpet Workshop, seven of whom traveled to Snow Farm.
Envision a half dozen men tending the dye pots. Madrim, master dyer of Khiva, throws freshly dyed skeins of Barglar (green leaves) overdyed with indigo, producing a rich green, against a wall where they stick, oxidizing, until ready to dry on nearby racks. Carpet weavers sit on low seats in front of looms, two to three women to the loom, weaving and tying knots of intensely rich dyed silk fiber, each rug taking two to six months to complete. Suzanni embroiderers craft intricate floral and geometric designs against dyed fabrics for garments and larger textile pieces. These are the artisans that came to teach at Snow Farm.
I took part in the natural dye program, "Working with Natural Dyes: A Rainbow of Silk Skeins". There were seven students, one translator, Dilorom Nishanova, the Uzbek artisan and master dyer, Madrim, and our American artisan partner, Kathy Hattori of Earthues, based in Seattle. It was brisk October weather for New England, lots of sun and sweaters as we joined in a shed off the main house to begin learning how to dye the Khiva way! Madrim, Dilorom and Kathy got everyone started with preparing the leaves for the Barglar dye pot: mulberry, camellia, onion skins, apple and grape leaves. Many of the leaves we used are indigenous in Khiva. We also prepared the dyebaths for black walnut, madder root, cochineal bugs and weld flowers. After soaking and simmering the raw dyestuffs according to Madrim's recipes, we dyed beautiful white silk skeins resulting in bright and rich hues of yellow, brown, orange and magenta. Some of these skeins we then overdyed with indigo.
Indigo is not only expensive but also treacherous for the artisans of Khiva to obtain as it most often comes from Afghanistan and Pakistan. The dyers need a source of black and although black walnut overdyed with indigo could produce black, the cost and difficulty of procuring indigo makes obtaining black still elusive. Kathy Hattori of Earthues worked very closely with Madrim performing dye tests during the after-hours trying to find a new way to obtain black that would be available and affordable to him and the Khiva dyers.
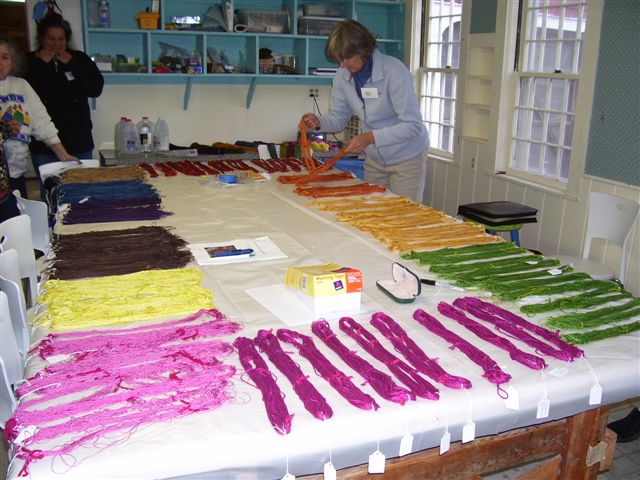
At the end of day two our group prepared a spectacular array of colored skeins. We arranged them by color around the worktable, each labeled with the dyestuffs and pertinent information for future reference. It was a color explosion! Students from the weaving and embroidery programs came to admire our results. Our group also visited their programs knowing that their embroidery and rug weaving were being created with the dyed fibers we were learning to make. After some group photos, hugs and goodbyes we dispersed; it was especially hard to say goodbye to our new Uzbek friends. At the common room many of the artisans and interpreters were gathered and I thanked them (the language barrier was challenging!) with a hug and a smile. Saying goodbye to Madrim was reflected in a closed hand on my heart and a hug–he knew what I meant. Dilorom (which means "peaceful soul" in Uzbek) has become a friend to me. Despite the language barriers, all of us shared humor, compassion and a love of dyeing. As I packed my car to leave I looked back to watch Madrim walk up the road alone to the dining hall and couldn't help but wonder when this exchange might occur again.
In May 2007, Michele Wipplinger, Pamela Mead Engberg and Elaine Ullman visited Khiva for two weeks, focusing on the suzanni embroidery workshop, working with a small group of Uzbek women, continuing the exchange and sharing techniques, colorways, and assistance with selling their crafts to the Western market in hopes of helping to sustain the craft and their livelihood. Uzbekistan–so far away yet so important to the global textile community.
In writing this article, I would like to give special thanks to Michele Wipplinger and Kathy Hattori of Earthues and to Elaine Ulman, Program Manager for the Uzbek exchange through The Institute for Training and Development (ITD), Amherst, MA. The Khiva Exchange was funded by the U.S. State Department's Bureau of Educational and Cultural Exchange.
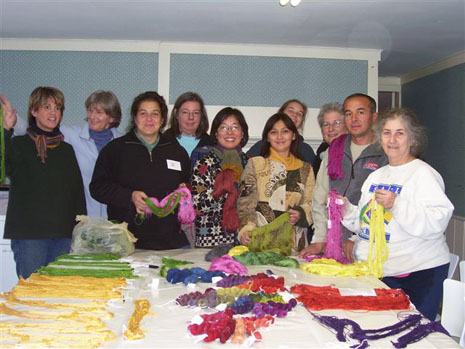
Dye Recipe for Yellow using Barglar (Green Leaves)
As used in Khiva, Uzbekistan
• Gather an assortment of fresh, green leaves such as apple, mulberry, camellia, and grape along with yellow or red onion skins. Pick out any brown spots or woody parts, and remove the short stem on the leaf. • Weigh out 100%-200% leaves (equal parts on the various species chosen) on the weight of the fiber and combine in a large dyepot, tossing the leaves to blend. Add enough water to cover and simmer for 45 minutes to extract the dyestuff. The dye liquor will be a light yellow-brown. • Strain out the leave and onion matter and return the dye liquor to the dyepot. Add a small amount of water if necessary to cover the fiber being dyed. • Enter the fiber into the dyepot and rotate during the first 30 minutes of dyeing to get an even color. Bring to 180°F and simmer for 45 minutes. Let the dyebath cool a bit then remove the fiber. • When overdyed with indigo, barglar makes a beautiful wine bottle green. |
![]() Photograph Copyright by Nancy Zeller |
Nancy and Jack Zeller
Long Ridge Farm
Westmoreland, NH 03467
603-313-8393
Website: www.longridgefarm.com