Brick Red with Morinda—A Dyeing Adventure in a Thai-Karen Community
By Sandra Loeffelmann
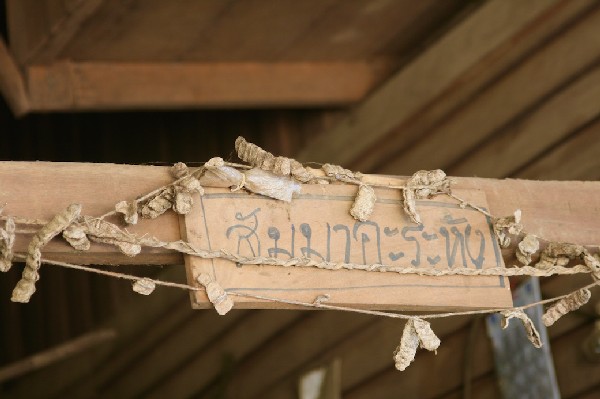
The Karen are an ethnic group living in South East Asia. There are about half a million Thai-Karen, but the majority of 7 million live in Myanmar (Burma), and have suffered oppression in the form of re-settlement, forced labor, lack of political representation and even denial of citizenship during the last sixty years. This has led another 140,000 Karen to move into Thailand as refugees. Most Karen are subsistence farmers who live in small and remote mountain villages, grow rice and vegetables, raise animals and keep an enduring textile tradition.
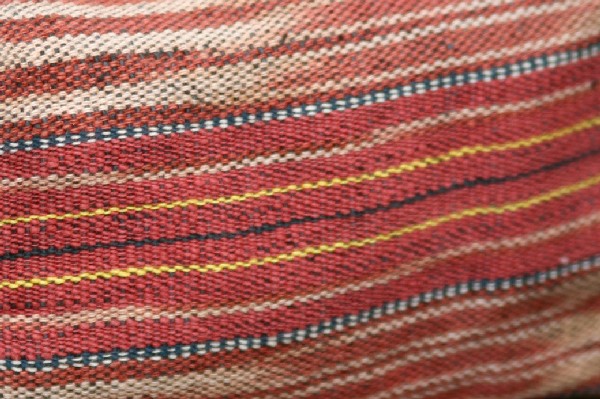
I had always been intrigued by the mysterious rain forest root which yields the pleasing brick red hues of Karen back-strap woven cloth. My Taiwanese friend Sylvia, who has lived in Thailand and has supported Karen weavers for the last 20 years, invited me to visit a remote village where this dyeing ritual is still practiced in a traditional way. We would be a part of the very special rite of finding, digging, and dyeing with this plant on the Chinese New Year and its New Moon! This mysterious root turned out to be Morinda citrifolia, a locally indigenous tree in the Rubiaceae family, related to coffee, bedstraw and ... madder. Now I was really excited!
Morinda citrifolia leaves and blossoms | The exposed root system after many harvests |
![]() |
![]() |
Photograph Copyright by Sandra Loeffelmann | Photograph Sandra Loeffelmann |
I knew it would turn out to be quite an exciting journey. But, exactly one month before the Chinese New Year / New Moon, we received a call informing us that the root harvesting and dyeing would take place the very next day! The villagers were desperate to dye their home grown organic cotton. They had not been able to do any dyeing for the last two years due to a tribal taboo: if a death occurs in the village, there should not be any dyeing for one month. Well, it seems there had been many deaths in this village during the last two years and they wanted to seize the window to dye before someone else died!
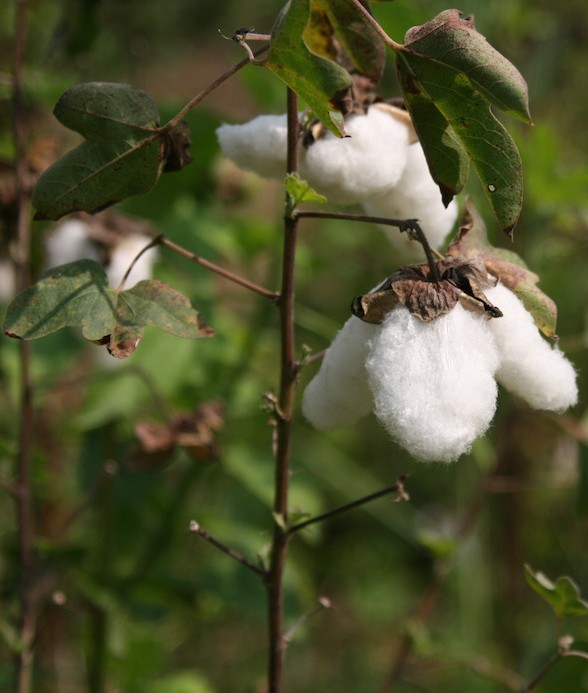
Traditional ginning of locally grown organic cotton | A heap of cotton seeds left after the ginning process ... fodder for the pigs |
![]() |
![]() |
Photograph Copyright by Sandra Loeffelmann | Photograph Sandra Loeffelmann |
Sylvia and I were learning about traditional natural dyeing in another village in northern Thailand, a long way from the Karen village, so after some back and forth, we decided to finish our current work and visit the Karen village at the original date, four weeks later. We were hopeful that someone would show us the Morinda citrifolia dyeing process then.
Fast forward four weeks. We arrived in the remote Thai-Karen village of Sor Kle Ka on a Thursday and to our "good luck" it was the day of no work which the villagers observe once a year. Since there is no phone signal, there was no knowing of this. Also, the villagers were not aware that we were coming. So we had no choice but to enjoy Karen hospitality, relax, eat, drink and do nothing but wait for the next day.
We stayed with Wannisa (or Nor Kor Por—her Karen name), a young Karen woman and her family. She is the only one of the younger generation in the village to continue the traditions of planting, spinning, dyeing and back strap weaving organic cotton. Unfortunately for us, she was out of root, but the neighbors were willing to share. They showed us the dried root and arranged to show us the dyeing process the next day.
The neighbor's dried and chopped roots | The soaked roots |
![]() |
![]() |
Photograph Copyright by Sandra Loeffelmann | Photograph Sandra Loeffelmann |
We were happy and ate our dinner of local rice, fresh eggs and wild harvested greens while eagerly anticipating the next day. To our dismay (the second time!) we were soon informed that the next door neighbors had changed their minds—we were not sure why.
Luckily, yet another villager agreed to instruct us in the dyeing process and so the roots were soaked over night. The next morning at breakfast, the woman came to us with a sad face and told us that she had gone up to the temple in the early morning and a village elder had told her not to dye today because it had not been 30 days since the last death in the village. With sunken hearts yet again, we accepted our fate the third time as the final blow, and sadly prepared to leave.
Not long after this, however, our spirits soared again when the village shaman came and informed us that he was allowed to show us the process because of an exception to the taboo: he was over 60 years old! So after all, we spent a most wonderful morning with this gentleman as we learned about all the layers of dyeing a brick red with the root of Morinda citrifolia.
1. The cotton is soaked in "sour water" (tannin rich water extracted from a local tree which we could not identify) for about a week, wrung out and dried. | 2. The yarn is then soaked in freshly made banana tree ash water. |
![]() |
![]() |
Photograph Copyright by Sandra Loeffelmann | Photograph Sandra Loeffelmann |
3. The material is then rubbed with the soaked and chopped roots for about one hour. | 4. Helpers rub some more. |
![]() |
![]() |
Photograph Copyright by Sandra Loeffelmann | Photograph Sandra Loeffelmann |
5. Until all the cotton is evenly coated in dye. | 6. Our teacher carefully chopping "sour" wood to cover the entire bottom of the pot. |
![]() |
![]() |
Photograph Copyright by Sandra Loeffelmann | Photograph Sandra Loeffelmann |
7. The bottom of the pot covered with "sour" wood; one little piece still missing. | 8. Then the yarn, roots and water are placed in the pot. |
![]() |
![]() |
Photograph Copyright by Sandra Loeffelmann | Photograph Sandra Loeffelmann |
9. The pot is covered with "sour" leaves. | 10. The cotton is heated over a roaring wood fire and boiled for one hour. |
![]() |
![]() |
Photograph Copyright by Sandra Loeffelmann | Photograph Sandra Loeffelmann |
11. The yarn is then removed, dried and stretched without rinsing. | 12. Because most dye materials have medicinal powers as well, Sylvia and I were instructed to rub our feet on the hot—burning hot—spent dye/mordant material. |
![]() |
![]() |
Photograph Copyright by Sandra Loeffelmann | Photograph Sandra Loeffelmann |
About the Author
Sandra Loeffelmann studied fashion, fiber arts and anthropology in Vienna, Austria and Eugene, Oregon. She has worked with natural dyes professionally for the last 20 years and is the owner of VERMILIO, a natural dye and fiber studio that has recently branched out to include naturally dyed, hand made + fairly traded accessories and clothing from around South East Asia. Sandra and her family split their time between Bellingham, Washington and Chiang Mai, Thailand.