How to Mordant Cotton—let me count the ways
By Donna Brown, Diane de Souza and Catharine Ellis
For the past 5 years, Diane and Donna have collaborated on projects using natural dye extracts. The goal has been to find consistent methods, which give predictable results. Given the long history of using natural dyes, there are many fiber-specific mordant methods. For cotton, there are two main approaches: 1) pre-soak in tannin and then mordant with potassium aluminum sulfate, and 2) mordant with aluminum acetate. In both cases, the mordant step can be followed by a chalk solution soak in order to fix the mordant prior to dyeing. The Art and Craft of Natural Dyeing by Jim Liles is a good resource for details.
from Table Rock Llamas Fiber Art Studio
Mordant used: 5% WOG Aluminum Acetate
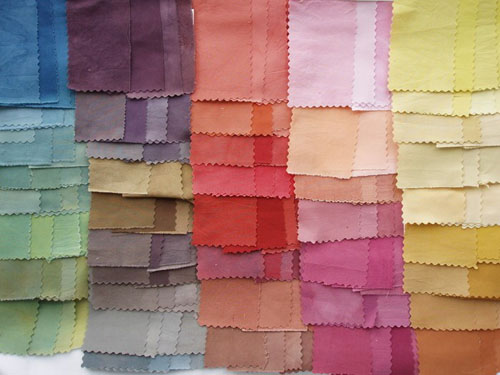
In order to develop a successful methodology for mordanting cotton, we conducted a series of experiments. (Detailed instructions for the preferred methods are provided at the end of the article). The first experiment compared the following 6 mordant recipes, derived from various sources (see References below):
•5% WOG aluminam acetate
•25% potassium aluminum sulfate
•8% tannin soak followed by mordanting with 25% potassium aluminum sulfate
•25% potassium aluminum sulfate and 6% WOG Soda Ash
•8% tannin soak followed by mordanting 25% potassium aluminum sulfate and 6% WOG soda ash
•8% tannin soak followed by mordanting 50% potassium aluminum sulfate and 6% WOG soda ash
The different methods were compared using a selection of natural dye extracts with cotton yarns, and a variety of cotton fabrics. The results indicated that the mordant recipe using 5% WOG aluminum acetate was the most effective. It provided comparable or better visual results than the other recipes, and has only one mordant step and one ingredient. Some of the more successful results were chestnut, cutch, fustic, myrobalan, madder, osage orange, tesu, and weld. Cochineal and logwood purple had the expected uneven coloration. Adding glauber salts to the dye pot helped to even the color. Until the fall of 2009 Donna and Diane used this method for mordanting cellulose.
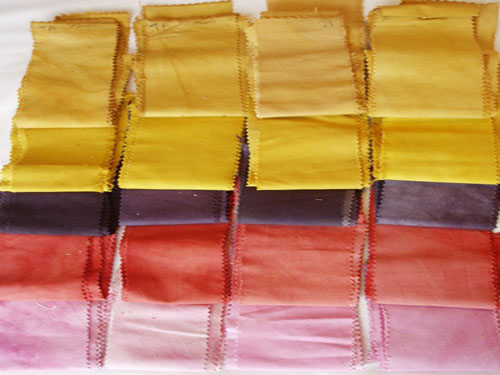
•Tannin 8% WOG ; 50% WOG Potassium Aluminum Sulfate and
6% WOG Sodium Carbonate (Liles—2 Steps)
•25% Potassium Aluminum Sulfate and 6% Sodium Carbonate; 8% Tannin;
repeat step 1 (Dean—3 Steps)
•5% WOG Aluminum Acetate
•50% Potassium Aluminum Sulfate and 6% WOG Sodium Carbonate
Dye extracts top to bottom: Fustic, Osage Orange, Logwood Purple, Madder (Rubea cardifolia), Cochineal
At that time, Donna, Diane, and Catharine Ellis scheduled two days for dye experimentation. Catharine participated in the 2008 International Shibori Symposium in France, and attended a demonstration by Michel Garcia. Mr. Garcia created an aluminum acetate mordant for block printing by mixing potassium aluminum sulfate and calcium acetate. Jay Rich in the Summer 2009 SDA Newsletter has reported the recipe and process from the Symposium. Rather than mixing an aluminum acetate mordant, Catharine adapted Mr. Garcia's recipe by making a 5% solution of aluminum acetate. As our cellulose mordant methods were different, we decided it would be beneficial to compare the aluminum acetate immersion method to the adapted recipe from Michel Garcia. This adaptation will be referred to as direct application aluminum acetate. Fabrics and yarns pre-treated with soymilk were included in the comparison.
The second comparison included the following:
•5% WOG aluminum acetate
•5% WOG aluminum acetate, fix with chalk
•Direct Application aluminum acetate
•Pre-soak in fresh soymilk, dry and then mordant with 5% WOG aluminum acetate
•Pre-soak in fresh soymilk, dry, direct application aluminum acetate
•Pre-soak in fresh soymilk, dry
The fabric and yarn were mordanted and dyed in 6 colors for comparison. Once dried and pressed, it was clear that all the mordant methods produced color, including the fabrics treated with soymilk. Mordanting with direct application aluminum acetate produced darker shades of color. The chalk-fixing step did not make a difference with the 5% WOG aluminum acetate process. Some of the samples were streaked, and everyone agreed that more care should be taken in rinsing out the chalk used to fix the alum acetate mordant. It was also agreed that more experimentation was necessary with different colors and cotton yarns to verify the results and compare Garcia's method to the direct application with alum acetate.
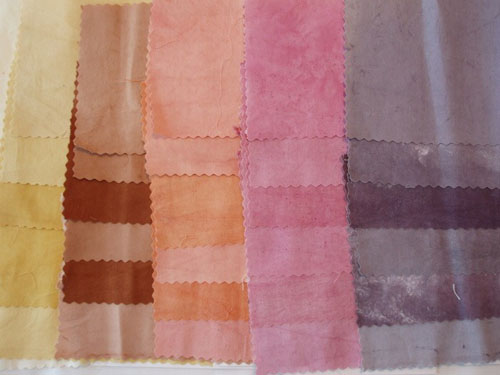
•5% WOG Aluminum Acetate
•5% WOG Aluminum Acetate fixed with chalk
•Direct Application Aluminum Acetate
•Pre-soak in fresh soymilk, dry then mordant 5% WOG Aluminum Acetate
(Note: Fustic is missing)
•Pre-soak in fresh soymilk; dry then Direct Application Aluminum Acetate
•Pre-soak in fresh soymilk, dry
Dye extracts from left to right: Fustic, Cutch, Madder (Rubea cardifolia), Lac, Logwood Purple
The third comparison included the following:
•Direct application but with Garcia's method for mixing aluminum acetate
•Direct application with aluminum acetate
•5% WOG aluminum acetate
•10% WOG aluminum acetate
•Adding glauber salts to the dye pot to even out the color
Again, all methods produced color. In general, the Garcia recipe was the darkest and the colors were comparable to using 10% WOG aluminum acetate by immersion. The Direct Application was lighter in color compared to the Garcia Recipe but darker then the 5% WOG aluminum acetate. The effect of the glauber salts was dye dependent. The lac, madder and cutch were more even, but it had a negative effect on brazilwood. In some cases, it also altered the resultant hue and value.
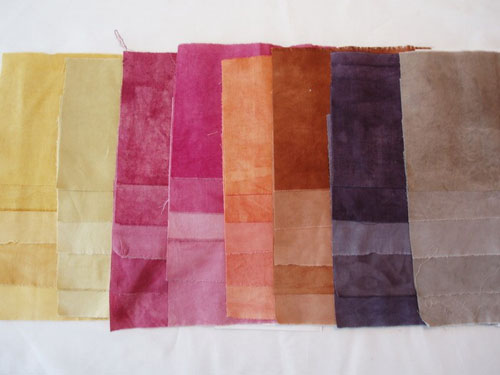
•Direct application using Mr. Garcia recipe for mixing Aluminum Acetate
•Direct application using a 5% Aluminum Acetate Solution
•5% WOG Aluminum Acetate
•10 % WOG Aluminum Acetate
•5% WOG Aluminum Acetate mordanted as the Direct Application fixed with chalk
Dye extracts from left to right: Fustic, Myrobalan, Lac, Brazilwood, Madder (Rubea cardifolia), Cutch, Logwood Purple, Quebracho Black
In reviewing the results of the cotton mordant experiments, we discovered a math error. The chalk solution used to fix the direct application aluminum acetate mordant was accidentally doubled in strength. This explained why rinsing those samples was difficult, but also raised a question about whether it affected the results of the experiment.
Therefore, a fourth comparison was carried out with the adjusted chalk mixture and the following:
•Direct Application but with Garcia's method for mixing aluminum acetate dyed within a day
•Direct Application with aluminum acetate dyed within a day
•Direct Application Garcia aged for a month
•Direct Application with aluminum acetate aged for a month
Again, Garcia's method produced darker shades of color, while the direct application aluminum acetate method produced a more even dye color. In both cases the fabrics aged for a month were significantly darker than the freshly mordanted fabric and yarn. In this comparison the aged samples mordanted by the 2 methods produced samples that looked more alike.
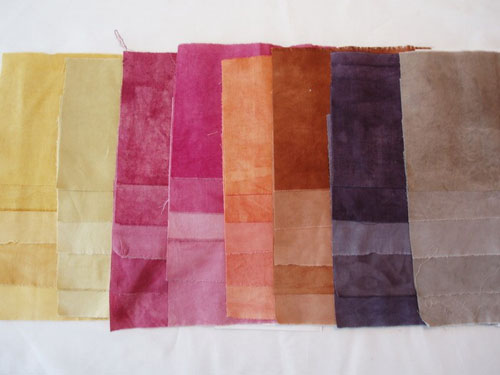
•Garcia recipe—dyed fresh
•Direct application using a 5% Aluminum Acetate Solution—dyed fresh
•Garcia recipe—cured 1 month before dyeing
•Direct application using a 5% Aluminum Acetate Solution—cured 1 month
before dyeing
Dye extracts from left to right: Brazilwood, Myrobalan, Fustic, Lac, Madder (Rubea cardifolia), Cutch, Himalayan Rhubarb, Quebracho Black, Logwood Purple
The primary goal for this study was to determine the best method for mordanting cellulose-based yarns/fabrics. The results of the study are complex, and conclusions depend on the weight assigned to the variables associated with each method—cost, time, complexity, water usage, dyes used, and items to be dyed etc. In economical terms, the 10% WOG immersion does not make sense. The Garcia and direct application methods have more steps, take more time, require special equipment for quick drying, and are difficult to apply with large quantities of fabric or yarn. On the other hand, they work well with small pieces of fabric, skein and fabric painting, and surface application of different mordants: iron or modifiers can be mixed with the alum acetate and paint then dye with one color to get different effects. For large quantities of fabric or yarn, the 5% WOG immersion mordant is more cost effective, both in terms of materials and time.
Below is a list of costs for comparison purposes. Water, fabric, and yarn type will affect amounts.
Method
Cost
Garcia
$1.75 (/solution, will mordant ~ 1 lb)
5% Alum Acetate - Immersion
$2.95 (/lb)
10% Alum Acetate - Immersion
$5.90 (/lb)
5% Alum Acetate - Direct Application
$3.50 (/solution, will mordant ~ 1 lb)
Chalk Solution - can be reused
$3.80 (/solution)
What advice do we have for others interested in this topic? Review available literature and be aware that some recipes are subject to the "grandmother syndrome" (that's how grandma did it). Document the methods you use both in terms of steps, recipes, and samples. The error in the chalk amounts would not have been found without a record trail of the original source and the modifications. Review your samples and document inadequacies. Determine areas of improvement and collaborate with others interested in your methods to identify possible solutions. Experiment, document your process, and determine if it is an improvement. Assess whether the improvement warrants the extra effort or cost that may be involved. We encourage you to experiment with natural dyeing and remember there are lots of effective methods. There is no one correct way, but rather, there is a method that will work for you.
Recipes for Mordanting Cellulose Yarn and Fabric
1. Preparation of yarn/fabric for mordanting:
Tie skeins in at least 3 places with loose ties.
Finish fabrics to avoid raveling.
Label right and wrong sides of fabric.
Label different yarn/fabric types if they are mordanted together.
2. Scour the fabric/yarn:
In some cases this is a fairly labor-intensive process, but should be done with all fabrics/yarns; even those sold as PFD (prepared for dyeing), as there still may be waxes and pectins that need to be removed before dyeing. Scour yarn/fabric in hot to boiling water to remove pectins and waxes, and scour according to the amount of dirt on the fiber. At a minimum, use a surfactant. Some yarns/fabric will require a cotton scour (1% based on the WOG) and soda ash (6% WOG) or washing soda. Continue to scour until water is clear.
3. Wet out the fabric/yarn (only if fabric/yarn is dry):
Wet with heat and a surfactant. Spin off or squeeze out excess water.
Surfactants: Synthrapol, Joy detergent, Dawn detergent.
Mordant recipes for cellulose fibers using an aluminum acetate solution
Michel Garcia's method (A) and recipe adapted from Michael Garcia's method (B)
A. Michel Garcia Recipe
1. Create an aluminum acetate mordant by mixing 50 grams aluminum sulfate and 50 grams calcium acetate in 1 liter of water (or equivalent).
2. Continue with Step 2 (Dip in aluminum acetate solution) below.
B. Direct Application aluminum acetate recipe
1. Make a 5% aluminum acetate solution. For example: Dissolve 10 grams aluminum acetate in 200 ml of water.
USE CAUTION when weighing aluminum acetate, which is a very fine powder. Use gloves and mask.
Note: Once you have prepared the aluminum acetate solution the procedure is the same for both methods
2. Dip in aluminum acetate (AA) solution (the solution can be at room temperature) for a few minutes (heavy fabrics need to stay longer) or apply aluminum acetate mordant with brush.
Note: The AA solution will keep for about a week if refrigerated and if the acid doesn't evaporate. Garcia recommends using a 'floating' cork or use a wine bottle and a cork that pulls out the oxygen.
3. Dry the fiber/fabric with heat. Clothes dryer, hair dryer, or a drying box will work. The dried fiber/fabric can be dyed immediately or aged.
4. When ready to dye: Fix the mordant by soaking dry, mordanted yarn/fabric in chalk/ cornstarch solution.
Mix 28 g of chalk, 4 liters of water, and 4-5 grams of cornstarch.
Heat solution to 160 F (the cornstarch needs heat to dissolve).
Note: the chalk solution can be kept and reused.
5. Rinse yarn/fabric in water.
6. The yarn/fabric is ready for natural dye; paint (dye can be thickened) and then steam or immerse.
Aluminum acetate mordant based on the WOG
1. Use 5% aluminum acetate on the dry weight (WOG) of the cellulose yarn/fabric.
USE CAUTION when weighing aluminum acetate, which is a very fine powder. Use gloves and mask.
Note: Double the amount of aluminum acetate for a 10% WOG mordant.
2. Weigh and dissolve aluminum acetate in boiling water. Add mordant into pot. Add scoured, wet yarn/fabric to mordant pot with enough water to cover the fiber in the pot. Slowly bring pot temperature up to a simmer for one hour. Stir regularly. Cool or let stand overnight.
3. Rinse yarn/fabric in water.
4. The yarn/fabric is ready for natural dye - paint (dye can be thickened) and then steam or immerse.
5. The yarn/fabric may be dried at this time, and stored until you are ready to dye.
Supplies available from Table Rock Llamas Fiber Arts Studio
References
Adrosko, Rita J. Natural Dyes and Home Dyeing. New York, NY; Dover Publications, 1971
Buchanan, Rita. A Dyer's Garden. Loveland, CO; Interweave Press, 1995
Crook, Jackie. Natural Dyeing. New York, NY; Lark Books, 2007
Dalby, Gail. Natural Dyes for Vegetable Fibers. Published by author, 1992
Dean, Jenny. Wild Color, New York, NY; Octopus Publishing Group Ltd, 1999
Fereday, Gwen. Natural Dyes. UK; British Museum Press, 2003
Grae, Ida. Nature's Colors: Dyes from Plants. Collier Macmillan, Canada; Macmillan Publishing Co., Inc, 1974
Liles, J. N. The Art and Craft of Natural Dyeing. Knoxville, TN; The University of Tennessee Press. 1990
Rudkin, Linda. Natural Dyes. Great Britain; A && C Black Publishing, 2007