Indigo Renaissance
By Caroline Harper
Indigo is experiencing a renaissance these plants are calling on us to work with them as growers, dye makers, natural dyers and textile artists, to bring their magical blue hues back into our world. I feel fortunate to be living in a time when a growing number of people like me are looking to reconnect with the source of things in our lives. Natural indigo is an antidote to the world of fast fashion, synthetic fabrics, chemical dyes, and the devastating impacts of the global textile industry on workers and the environment. It is refreshing to grow indigo plants, produce natural indigo dye from those plants, dye natural fabric with that indigo, and share those products with appreciative and passionate customers. It is a unique pleasure to work with those who participate in a natural dyeing workshop or even an indigo harvest followed by a dyeing workshop with a fresh vat. I have no doubt that this plant and its magical shades of blue have a restorative effect on people's lives.
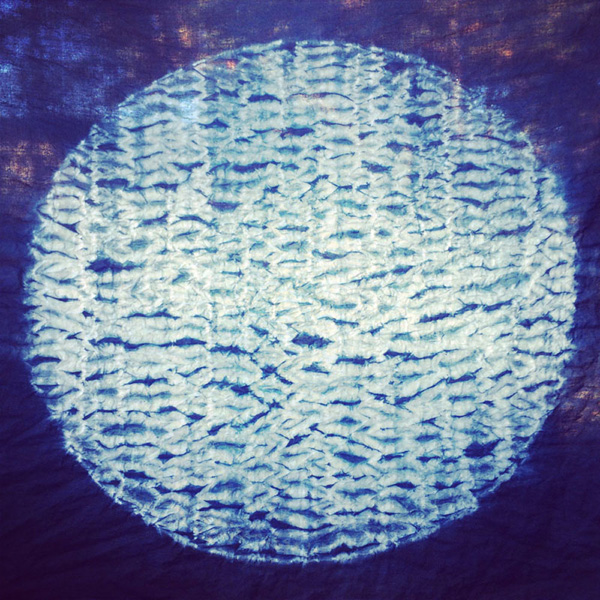
Becoming a textile artist working with indigo has been a natural journey along my soul path. Growing up in Nantes, France (Brittany) I became aware of our long history with natural dyes, specifically woad (Isatis tinctoria) or pastel as we call it, once centered in the Toulouse area of the southwest. Since moving to South Carolina more than 25 years ago, I have learned of the central role that Guatemalan indigo (Indigofera suffruticosa) played here in the Lowcountry plantation economy of the 1700's. I received my degree in fine arts from the University of South Carolina in the 1990's and embarked on a career as a graphic designer without any real exposure to indigo. Here in South Carolina, indigo is something that students learn about in elementary school. They are taught that our state flag was originally dyed with natural indigo grown by slaves on plantations, and that a young entrepreneur named Eliza Lucas Pinckney developed indigo into one of the top exports out of Charleston up to the Revolutionary War. Still, with all of this history, indigo is not alive in our culture today. We hope to change that by co-creating a community of indigo growers, dye makers, dyers, textile artists, and indigo enthusiasts with a shared vision of an indigo renaissance.
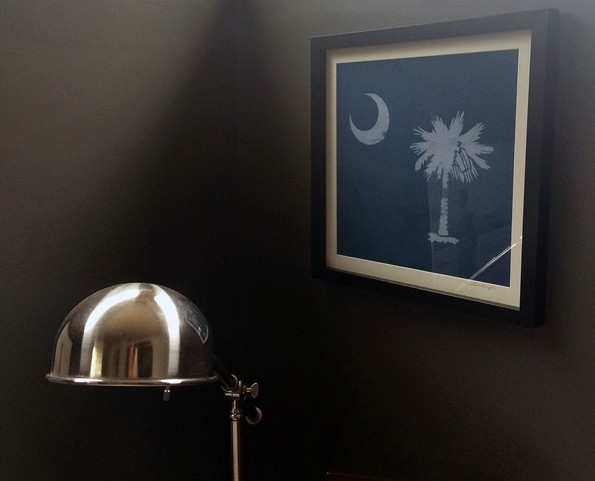
As a graphic designer I worked with digital art using a mouse and a keyboard, yet I continued to create with my hands, painting with acrylics and working with my daughter Elle on art projects. For several years I ran a small fashion business selling Cabi women's clothing in trunk shows (www.cabionline.com). Through that business I learned about community-based marketing and sales and presentations to small groups. Still, there was no natural dye in my life. When my mother passed away I felt I'd lost my moorings. I found myself searching for meaning and my true calling.
I remember clearly the day that indigo opened my eyes to new possibilities in my work. One day I met a sweet, smart woman who said she had noticed the photographs I had taken for a new restaurant. She said she liked my creative energy and the way I worked. Peg Averyt invited me to work with her to develop an online marketing strategy for her business, Finleaf Gallery. It was here that I was surrounded by hand crafted goods made by artisans from around the world, including Shibori pieces dyed with natural indigo.
I had always had a fascination with Japanese culture, especially art. I kept coming across references to Shibori and began to learn about this ancient tradition of resist dyeing with indigo. For centuries, Japanese kimonos and other textile goods were produced by wrapping cotton or silk fabric around a bamboo pole and tying folds of the fabric with a cord to create patterns with the indigo dye. It was then that South Carolina indigo began to be something more about the present to me, and not just a history lesson. Through my research I learned of a master dyer who led intensive workshops at his silk and indigo farm in the mountains outside of Tokyo. Somehow I felt if I could meet him and experience these traditions I would figure out what I was supposed to be doing. I launched a Kickstarter campaign to help raise funds for the tuition from my friends and family, and the support I received was overwhelming and heartwarming. Each supporter received either a Shibori indigo handkerchief, scarf, t-shirt or pillow, depending on their giving level—so it allowed me to test my newfound skills and reward those who believed in me.
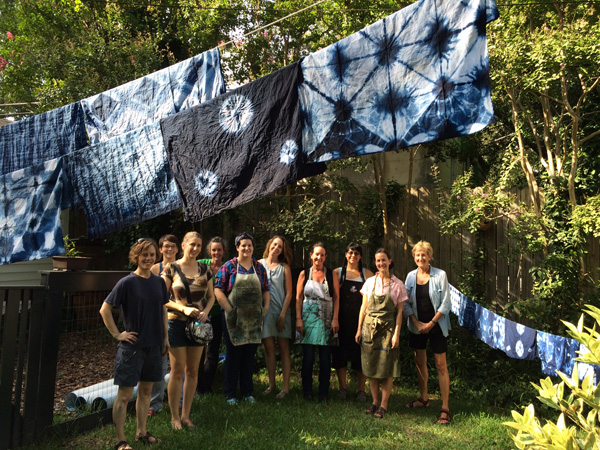
Upon my return I immediately began working with indigo and natural fabrics to develop a line of products ranging from shibori silk scarves to framed mokume prints. I set up a booth at my local farmers' market in Columbia, South Carolina. I began teaching indigo dyeing workshops in my backyard and eventually had my shed (and urban chicken coop) converted into a studio. Now in my third year, I have refined my product line and increased sales both on-line and at craft shows in the Carolinas. I have expanded my offering of workshops to include a wider range of natural dyes, eco-printing, and harvesting indigo to make a fresh vat from the plants. Perhaps most importantly, my husband and I have partnered with farmers/friends to begin growing Guatemalan indigo and making dye powder on a farm near Kingstree, South Carolina, an area which was known for the quality of its indigo in the 1700's.
The most inspiring moments for me are the connections made in markets and workshops with people who really appreciate the beauty and hands-on creativity of a plant-based color. It feels good when people tell me I m talented and that my work inspires them. My first sale at our local Soda City Market was deeply meaningful to me. It was a little after the market opened on a Saturday morning in the fall, and a well-dressed woman looked at my booth filled with blue products and walked past, then came back and looked very closely at a set of pillows I had made from linen dyed with indigo. She said she was visiting from Atlanta on a business trip and had decided to come to the market. The indigo pillows reminded her of her home country of India, which has a culture with continuous use of indigo for thousands of years. She bought both pillows for her living room and we were both happy.
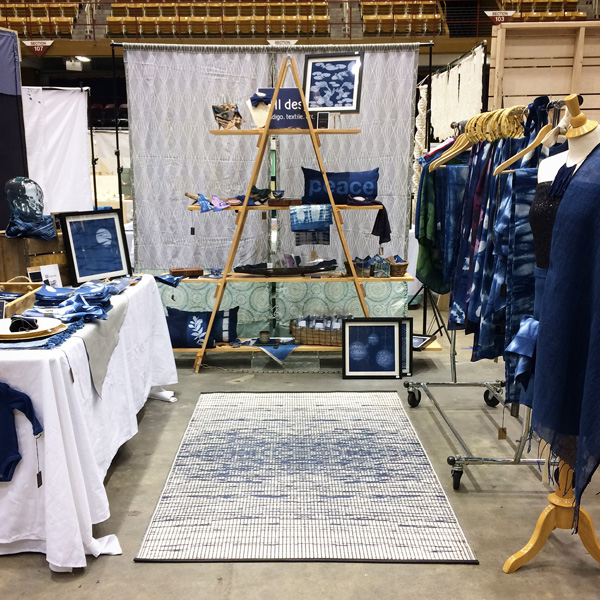
Harvesting plants in the field with a group of indigo enthusiasts has been another highlight for me. We planned our harvest party for the optimum time, when the plants were just starting to flower in September/October. A group of 18 enthusiastic farmers, natural dyers, and indigo lovers gathered at the farm with the excitement of knowing that they were playing a key role in the revival of South Carolina indigo. We harvested leaves and stems from about 500 plants growing on ¼ acre of sandy loam soil, leaving enough on each plant for the flowers to go to seed. We bundled and weighed a total one-pound bundles. We submerged them in warm water in three 150-gallon stock tanks (cattle troughs) and then weighted them down with bricks and mesh screens, covered them with tarps, and let the leaching and fermentation process begin. The harvesting party then included a wonderful lunch to celebrate the harvest and the community of harvesters (like a French wine harvest). Each of the harvesters then had the opportunity to dye their own natural fabrics in a fresh vat made from an earlier harvest.

Our first season yielded about 20 lbs of powdered dye from two harvests; and this growing season we hope to double this to 40 lbs from ½ acre of plants. The plants thrive in the heat of summer and do not have any real pests to speak of, so they are grown organically. The most challenging part for us was reducing the water with repeated skimming to get to the dye sediment settled at the bottom. We then removed the blue mud into trays lined with Oznaburg linen cloth that was traditionally used in the drying process. For the final drying we tied the cloth into bags and hung them from an antique pine indigo drying rack (but hanging them from trees works just as well). We documented the entire dyemaking process in a video (http://chidesignindigo.com/shortfilms/), though it is truly a matter of trial and error to find what works best for each crop, each site, and each climate.
We now offer a limited amount of powdered South Carolina indigo dye to natural dyers under the label Blue Gold Indigo (http://chidesignindigo.com/boutique/4oz-south-carolina-grown-indigo-dye-powder). I use the majority of the dye in my own products.
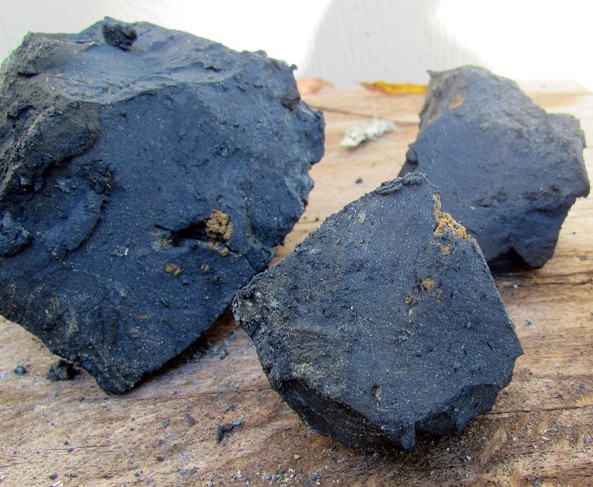
Leading natural dyeing workshops is one of my favorite parts of the business—I like teaching art and giving people the opportunity to play with the dye and forget their worries for a few hours. It's truly remarkable to see how the mood can shift from strangers being kind of quiet at the beginning, to a group that opens up with "ooohs" at their own creations and "aaaahs" at those of the others. Participants love to see what they've created based on what I teach them, and how each person s design differs. The harvest workshops in the fall attract a more serious crowd of gardeners and history buffs who are eager to go to the farm, harvest indigo stems and leaves, and make a fresh vat for dyeing.
Most natural indigo dye powder still comes from Bengal, India, the leading producer since the industry was shifted there by the British after the Revolutionary War. Sparking an indigo renaissance in America will require rerstarting the dye production and scaling it up for wider commercial use. There is clearly a steep learning curve involved in reinventing indigo for the 21st century. The process includes plenty of learning as we go with a trial-and-error approach: our first batch of dye came out more gray than blue and the seeds we collected from the second year's crop did not germinate. There are serious bottlenecks since the plant cuttings cannot be stored after harvest—the dye must be made on the farm from fresh cuttings, so there are limitations in the size of the vats, the heating of the water, and labor for skimming and drying the dye. We must address these challenges to modernize the process.
We are thrilled to have a growing community of growers, dyers and textile artists in the Southeast who are ready, willing and able to form an indigo guild and bring nature's blue back into people's lives. Donna Hardy, Leigh Magar, Kathy and Bill McCullough and others are putting South Carolina indigo back on the map.
We encourage all natural dyers with a passion for being part of the indigo renaissance to join us. Explore our website, sign up for the newsletter, order some Blue Gold SC Indigo dye powder (when supplies are available), help spread the word, and share your ideas. Come visit us here in Columbia, South Carolina and join us for a workshop. Long live indigo!
Chi Design, launched in the fall of 2014, focuses on producing textiles for home goods and fashion accessories, hand-dyed with natural indigo, and made with natural fibers (cotton, silk, linen). Caroline Harper traveled to Japan in 2014 to study resist-dyeing methods such as shibori, mokume and katazome and has been practicing them in South Carolina since then. She sells many of her products at craft shows; on-line through her website and Amazon Handmade; and in small boutiques and galleries. Caroline shares her passion for indigo, shibori and other dyes from nature by hosting workshops for various levels of interest and skill. She is a native of France where historically there was a strong industry of blue dye from a plant Woad. Caroline is now harvesting small batches of South Carolina indigo plants (Indigofera Suffruticosa), making fresh-leaf vats and powdered dye that can be stored for a long period of time and used later.